
RP Disintegrator
Sanitary Angled Hammer Mill
The Original and Still the Standard
The RP Disintegrator is our original, Rietz-designed, angled hammer mill, widely used in the food industry for a diverse range of applications. The signature, angled design lends itself to applications where operational versatility is required, providing quick and easy access to internals for cleaning, changing the setup, and maintenance. As our most versatile hammer mill, the RP Disintegrator is designed around three key tenets: versatility, simplicity, and cleanability.
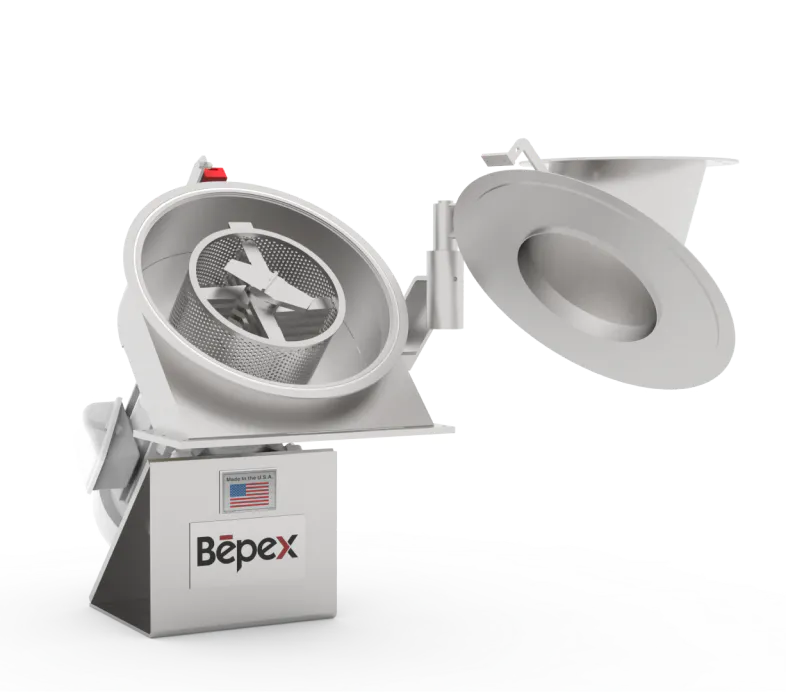
Versatility
Processing capabilities include coarse grinding, homogenizing, delumping, shredding, pureeing, finishing, and pulping. From dry solids to slurries, whole pineapples to fine powders, the RP Disintegrator can be equipped to handle nearly anything you can throw its way. Whether wet or dry, large or small, the RP Disintegrator will handle it all.
Simplicity
Widely used across the food, chemical, and mineral industries, simplicity is the guiding principle behind our proven design. Simple design is easy to install, use, and maintain. Simple design doesn’t break. Simple design has established and built the RP Disintegrator’s reputation for quality and performance for decades of meeting tough processing challenges.
Cleanability
The RP Disintegrator’s signature angled design provides easy access to internals for product change-over, maintenance, or cleaning.
Advantages
Endless Design Options
Quick change sizing screens makes achieving different results easy. A variety of hammer designs are available to match your application, including blunt impact hammers and sharpened knives. Thousands of possible screen designs and hammer combinations are possible.
Direct Drive Motor
The specially designed direct-drive motor means screen and hammer changes are done in minutes. Direct drive operation eliminates the need for unnecessary drive components, improving reliability and reducing maintenance and downtime. Our standard motor also is inverter duty rated, so you can adjust the speed via a variable frequency drive to dial in each application.
Easy, Quick Application Change Overs
You are 30 seconds away from internal access after an operation ends, even with a lockout/tagoutprogram. A single tension-spring clamp typically secures the cover to the assembly. On larger units, a hinged swing open cover makes access safer and easier. Easily swap out screens or hammers, dial in the speed, and you’re ready to run.
Compact Footprint
The angled design allows even our largest machines to fit in tight operating spaces. With a maxheight differential of 40 inches from inlet to outlet, the RP Disintegrator can fit into nearly any available space.
Sanitary Construction
Sanitary construction is our baseline, following USDA/FDA requirements. Higher grade or custom finishes are available, from 4A to mirrored finish.
How does it work?
Our most versatile hammer mill, the RP Disintegrator is designed with both flexible operations and easy maintenance in mind.
Quick internal access allows for setup changes between batches. Few removable components make cleaning quick and easy. A variety of easy-to-change screen and hammer designs are available to match specific applications.
Combine its operational flexibility with the RP Disintegrator’s small footprint, reliable direct-drive design, and processing efficiency and you have a workhorse mill that processors have relied on for decades.
In a typical application, material to be milled enters above the hammer assembly via an inlet chute or piped inlet.
The rotating hammers or knives begin imparting force or shear on the material. A 360° sizing screen surrounds the rotating hammer or knife assembly.
The material is forced into a thin layer around the periphery of the hammers and begins contacting the sizing screen.
Particles of the material that are reduced to spec will pass through the openings on the sizing screen. The particles that are still too large reflect off the screen and back into the path of the rotating hammers for additional grinding.
Once through the screen, material is discharged either via a chute or piped connection.

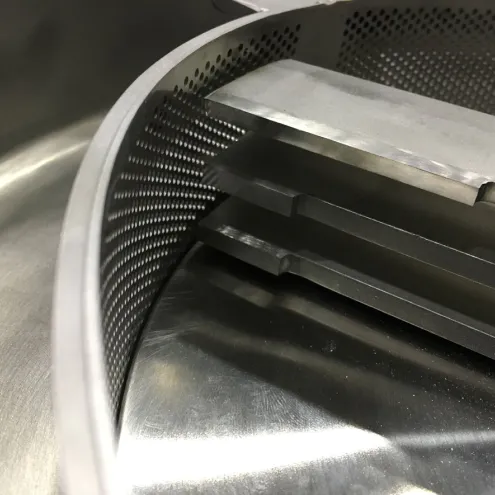
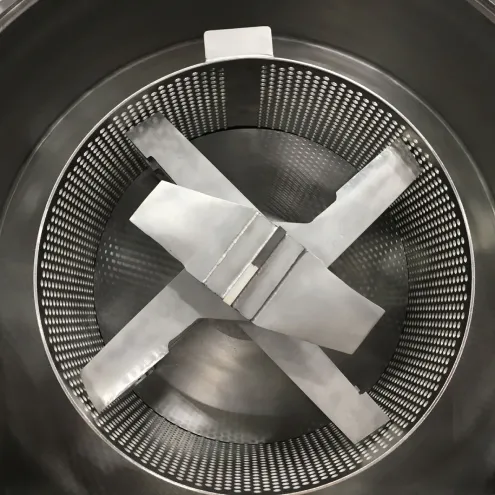
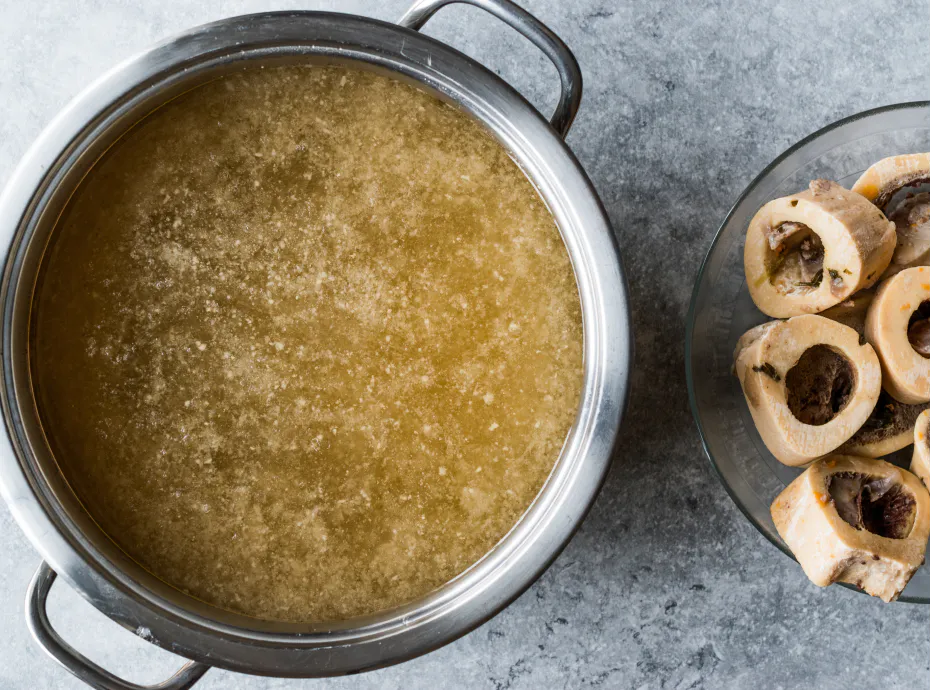
Meat and Bone Broth Cooking
Bepex helps convert broth production and pressure cooking from batch to continuous processing – improving product quality and profitability. Bepex also offers equipment to grind and reduce blocks of meat, tissue, and bone into a consistent feed stream ahead of cooking – further increasing production efficiency.
Learn More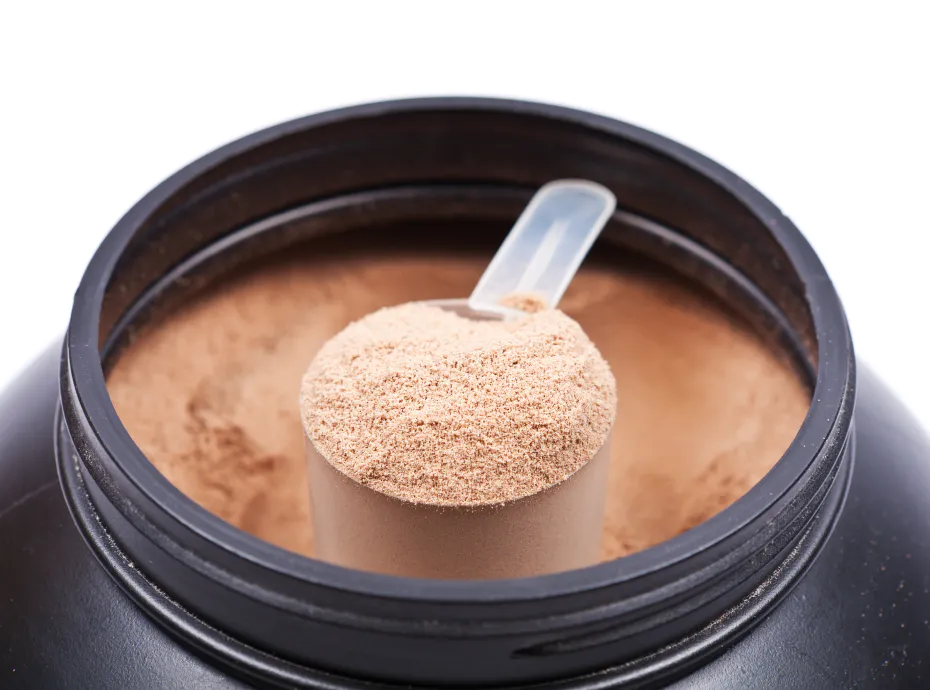
Plant Based Proteins
Bepex offers the most energy efficient, cost effective and environmentally friendly systems for processing plant-based production. Bepex systems require less energy and create less emissions. Plus they provide more control over protein modification, resulting in a higher quality product.
Learn More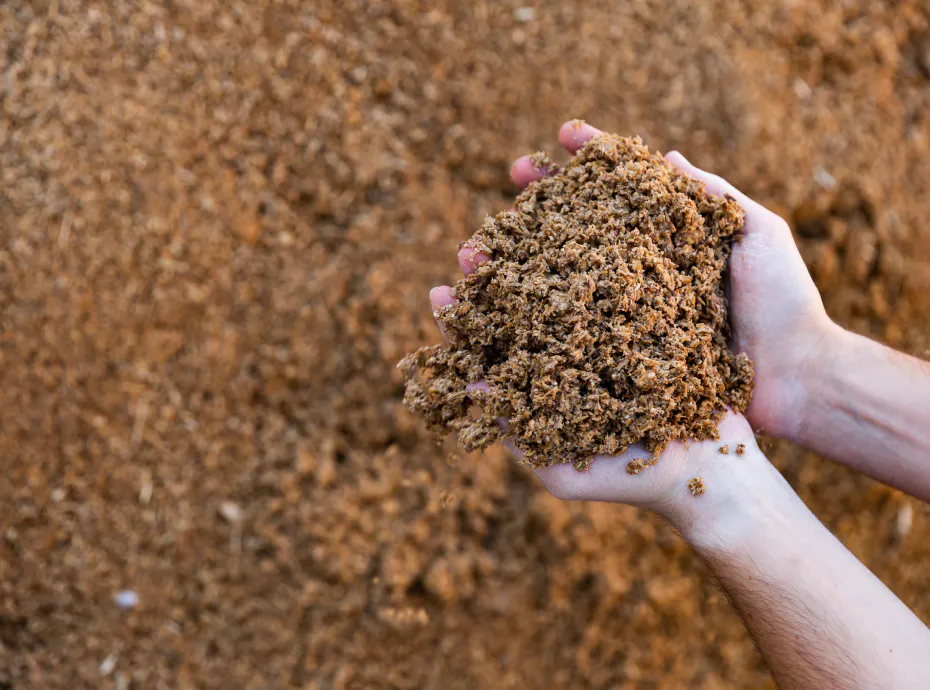
Pomace
Bepex transforms “waste” pomace into high-value protein products. Bepex offers a total solution to ensure consistent feeds, wring water from the pomace, and dry the wet cakes into powder or small granules. That improves efficiency and product quality, while lowering costs and reducing emissions.
Learn MoreA Legend – and Legacy – in Milling .
Originally designed and built for the California produce industry by Rietz Manufacturing – a Bepex predecessor company – the Disintegrator product line is synonymous with robust, reliable equipment for the food processing industry.
Years of experience and improvement have built on that legacy. So now, decades later, food processors still rely on the RP’s heritage of quality, reliability, durability and value.
Find out more from a Bepex process expert.